Spezialbohrgetriebe Explained: The Hidden Powerhouse Behind Precision Drilling
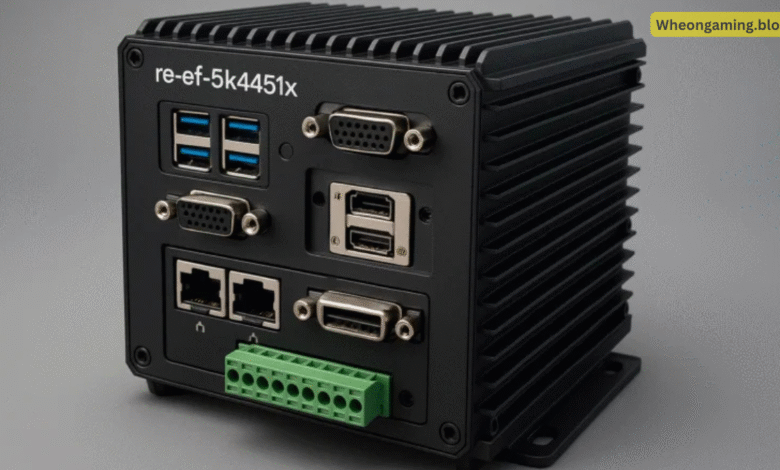
Introduction to Spezialbohrgetriebe: The Backbone of Specialized Drilling
When it comes to the high-performance world of industrial drilling, one term that often surfaces—yet remains elusive to the general public—is Spezialbohrgetriebe. While the word might sound intimidating to non-German speakers, it’s essentially referring to special drilling gearboxes—custom-engineered gear systems used in highly demanding drilling operations.
These gearboxes are vital in sectors ranging from oil and gas to tunnel boring, aerospace, and even advanced CNC machinery. Their job? To convert power into precise motion under extreme stress conditions, ensuring optimal performance and minimal downtime. Spezialbohrgetriebe are the unsung heroes of many major infrastructure and technological developments.
Let’s explore the specialized engineering, application, innovation, and future of these mechanical marvels in a casual professional and expert tone.
What Exactly Is a Spezialbohrgetriebe?

The term “Spezialbohrgetriebe” translates to “special drilling gearbox” in English. These are not your everyday gearboxes found in cars or home appliances. These are industrial-grade, high-torque, customized gearboxes engineered for precision under extreme conditions.
What sets a Spezialbohrgetriebe apart is its ability to handle specific drilling tasks that require unique torque curves, rotational speeds, and directional stability. Whether you’re drilling through granite or sub-sea rock formations, these gearboxes ensure that your equipment can handle the pressure—literally.
They are usually custom-built for machines such as tunnel boring machines (TBMs), deep-well drilling rigs, or even mining equipment. The customization includes everything from the type of materials used to the way torque is distributed across the machine.
In many cases, companies work hand-in-hand with gearbox manufacturers to design a system that fits their drilling needs to a tee. It’s not a plug-and-play solution; it’s bespoke engineering.
Engineering Principles Behind Spezialbohrgetriebe
Understanding the design of a Spezialbohrgetriebe requires some mechanical insight. These gearboxes are usually multi-stage planetary or helical gear systems, allowing for compactness while maintaining high power transmission efficiency.
The first core principle is torque amplification. When a drill needs to penetrate hard materials, it requires significant torque. A Spezialbohrgetriebe multiplies the input torque from a motor so that the drill bit can cut more effectively.
Secondly, load balancing is essential. These gearboxes are designed to distribute loads evenly, preventing wear and tear on individual gears or shafts. This increases lifespan and reduces maintenance costs.
Lastly, material strength and thermal dynamics play a crucial role. Spezialbohrgetriebe are often made from alloy steels and are heat-treated for durability. They also include cooling systems or are designed to dissipate heat quickly, as overheating is a common issue during continuous drilling operations.
Real-World Applications of Spezialbohrgetriebe
The use of Spezialbohrgetriebe spans various sectors, each with its unique challenges and requirements. One of the most common industries is tunnel construction. Here, tunnel boring machines need to work for months under tremendous stress, and without a robust gearbox, they simply wouldn’t function.
Another key application is in offshore oil drilling. In this scenario, gearboxes must operate under harsh environmental conditions like saltwater corrosion, high pressure, and volatile temperatures. Spezialbohrgetriebe used here are often sealed, reinforced, and made with marine-grade materials.
Additionally, mining operations in remote and rugged areas rely on these specialized gearboxes. Whether it’s rotary drilling or percussive systems, the gearbox determines the speed, force, and depth at which machines can operate.
Even renewable energy, especially geothermal drilling, has begun integrating these high-performance gear systems. As we dig deeper into the Earth for sustainable energy sources, the role of Spezialbohrgetriebe becomes even more critical.
Customization: The True Strength of Spezialbohrgetriebe
Off-the-shelf gearboxes rarely cut it when it comes to demanding drilling environments. That’s why customization is a defining feature of Spezialbohrgetriebe. Manufacturers work closely with engineering teams to define every aspect—gear ratio, output shaft design, lubrication system, and even smart monitoring technology.
Custom gearboxes are engineered based on several variables: material being drilled, depth of the bore, ambient temperature, expected load cycles, and the type of drilling equipment being used. The result? A product that works seamlessly with the host machine, delivering better efficiency, reduced wear, and optimal performance.
Some of the most advanced gearboxes now come with IoT sensors, which provide real-time data on heat, vibration, and torque. This smart feedback loop allows operators to adjust parameters or perform predictive maintenance, reducing the risk of sudden failures.
Challenges in Designing and Manufacturing Spezialbohrgetriebe
As with any high-precision equipment, designing a Spezialbohrgetriebe comes with challenges. For one, achieving the ideal balance between size and power is difficult. More power generally means larger gear systems, but space is often limited in compact drill designs.
Another key challenge is vibration and shock absorption. When drills hit dense material, shock waves travel back into the system. If the gearbox isn’t built to absorb these, it can crack or misalign, leading to system failure.
Also, environmental resistance is no small feat. The gearbox needs to withstand water, dust, chemicals, and extreme heat or cold. Hence, sealing systems, anti-corrosion coatings, and advanced lubrication all become crucial aspects of the design process.
Lastly, there’s the issue of cost and lead time. Customized systems are expensive and take time to design and produce. Companies often have to plan well in advance, which is not always feasible in fast-paced industries like mining or construction.
Advantages Over Standard Gear Systems
Spezialbohrgetriebe offer numerous advantages over traditional gear systems. First and foremost, they provide greater torque efficiency, allowing drills to operate at optimal levels even under adverse conditions.
Another advantage is durability. While standard gearboxes may fail or wear out quickly in heavy-duty environments, Spezialbohrgetriebe are built to last. Their longer lifespan justifies the higher upfront cost through reduced maintenance and downtime.
Also, the custom fit means there is less energy loss. Every part of the gearbox is designed to work in harmony with the machine, which enhances productivity and reduces energy consumption—something that’s becoming more important in today’s eco-conscious world.
In high-precision industries, these gearboxes also offer better control. With fine-tuned ratios and smart sensors, operators can make micro-adjustments during operation, something that’s virtually impossible with standard systems.
Innovations and the Future of Spezialbohrgetriebe
The future of Spezialbohrgetriebe looks incredibly exciting. With the advent of AI and machine learning, gearboxes are becoming smarter, capable of self-diagnosing issues before they become critical.
3D printing is also entering the scene, allowing for faster prototyping and even customized gear shapes that were previously impossible to manufacture using traditional methods.
Moreover, composite materials are being explored to reduce weight without compromising strength. These next-gen gearboxes will likely be lighter, more energy-efficient, and easier to maintain.
Another exciting frontier is the integration with renewable technologies. As we move toward cleaner energy, gearboxes will need to adapt to newer drilling applications, like geothermal wells or deep-sea mineral extraction.
Maintenance and Lifecycle Considerations
Proper maintenance is key to the longevity of any gearbox, and Spezialbohrgetriebe are no exception. However, because these systems are built for endurance, their maintenance cycles are generally longer and less frequent than standard systems.
Still, predictive maintenance is gaining traction. Using onboard sensors, operators can monitor metrics like temperature spikes or torque fluctuations and address minor issues before they escalate. This not only prevents catastrophic failure but also extends the life of the entire system.
Routine tasks include lubrication checks, seal inspections, and vibration analysis. Some systems are even automated to perform diagnostics and report via cloud-based dashboards.
Throughout its lifespan, a well-maintained Spezialbohrgetriebe can function reliably for over a decade, especially if it is regularly monitored and updated with the latest firmware and system optimizations.
Environmental and Safety Implications
Spezialbohrgetriebe play a pivotal role in safety. A failing gearbox in a high-risk environment can lead to dangerous consequences, including machinery collapse or operational failure. That’s why these gearboxes often meet or exceed strict industry safety standards.
From an environmental standpoint, more efficient gearboxes reduce energy consumption and lower carbon emissions. In industries like geothermal drilling, where environmental integrity is crucial, using a specialized, energy-efficient gearbox can make a significant difference.
The materials used in these systems are also evolving. Eco-friendly lubricants, recyclable metals, and low-emission coatings are becoming standard as companies look to reduce their environmental footprint.
FAQs About Spezialbohrgetriebe
Q1: What industries commonly use Spezialbohrgetriebe?
A: Industries like tunnel construction, oil and gas drilling, mining, aerospace, and renewable energy commonly use these gearboxes due to their specialized performance under tough conditions.
Q2: How long does a Spezialbohrgetriebe last?
A: With proper maintenance, these gearboxes can last 10–15 years or more, depending on operational intensity and environmental factors.
Q3: Are Spezialbohrgetriebe more expensive than standard gearboxes?
A: Yes, they are typically more expensive due to their custom engineering and high-performance capabilities, but the cost is offset by longer lifespan and reduced downtime.
Q4: Can Spezialbohrgetriebe be retrofitted into existing machines?
A: In many cases, yes. However, the gearbox must be custom-designed to fit the specifications and constraints of the existing machine.
Q5: Are there eco-friendly versions of Spezialbohrgetriebe?
A: Absolutely. Many modern manufacturers now offer environmentally friendly options, including biodegradable lubricants and recyclable materials, along with improved energy efficiency.
Conclusion
The Spezialbohrgetriebe is a powerhouse of precision engineering, combining durability, customization, and performance into one essential component. From deep-sea oil rigs to the tunnels that connect our cities, these gearboxes silently and reliably keep things turning.
Whether you’re an engineer, contractor, or just a tech enthusiast, understanding the role and capabilities of Spezialbohrgetriebe opens a new window into the machinery that powers our world.